Our industry-leading, high-speed industrial robots include high-payload, extended-reach, ultra-maneuverable seven-axis and unique 15-axis dual-arm robots.
Manutenzione preventiva e retrofit dei robot industriali
I robot industriali svolgono compiti di primaria importanza in diversi ambiti della produzione automatizzata. Fermi tecnici possono essere affidabilmente evitati anche quando i manipolatori e i controllori sono in funzione da molti anni o addirittura decenni. Per farlo sono però necessarie strategie di manutenzione su misura.
La norma DIN 31051, applicabile anche ai robot industriali, suggerisce varie soluzioni e descrive i principali tipi di manutenzione come correttiva, preventiva e predittiva. La manutenzione correttiva prevede la sostituzione di parti danneggiate e la riparazione dei componenti difettosi in caso di un fermo. Questo tipo di fermo non pianificato è estremamente costoso per le aziende. L’esperienza dimostra anche che puntare sulla manutenzione correttiva può essere causa di un’usura precoce della macchina.
Gestione della manutenzione preventiva
In base alla DIN EN 13306, 7.1, lo scopo della manutenzione preventiva è di ridurre la probabilità di episodi di fermo macchina o ridotta funzionalità. In sistemi con robot industriali la probabilità di malfunzionamenti è direttamente legata al ciclo di vita del robot e può essere sensibilmente migliorata ricorrendo all’adozione di soluzioni di manutenzione preventiva. In una prospettiva di lungo termine, la manutenzione preventiva preserva il valore dei beni strumentali e contribuisce così a migliorare il bilancio di lunga durata. Una verifica annuale da parte del produttore dei robot documenta le condizioni del sistema, fornendo le basi per la creazione di piani di manutenzione.
La manutenzione preventiva porta anche vantaggi economici tangibili. Ipotizzando che annualmente si abbia un incremento dell’efficienza pari al 0,25% e 4000 ore operative, i fermi necessari alla manutenzione della macchina saranno ridotti di 10 ore. Ad un costo orario di 2500 € per macchina, ne deriva un risparmio annuo di 25000 €.
In aggiunta, il significativo miglioramento nella disponibilità dei sistemi comporta una notevole riduzione dei costi di magazzino, in quanto i ricambi di molte parti critiche non devono più essere tenuti a stock.
Retrofit
L'elevata disponibilità e un lungo ciclo di vita dei robot industriali significano anche un migliore ritorno sugli investimenti. Un sistema progettato per un’operatività complessiva compresa tra gli otto ed i dodici anni, oggi ha spesso una durata variabile da 16 a 24 anni. Tuttavia, il ciclo di vita effettivo di un robot è rimasto invariato da cinque a otto anni, per cui si rende necessario considerare la possibilità di retrofit o nuove acquisizioni.
In alternativa a nuovi costosi acquisti, che spesso comportano un cambio di generazione della macchina e quindi spese aggiuntive per la riprogrammazione e la formazione del personale, i produttori di robot offrono anche unità sostitutive e programmi di retrofit sistematici finalizzati a ridurre al minimo le interruzioni della produzione. L'uso di un modello identico non implica "grandi cambiamenti nelle macchine" ai fini della Direttiva macchine 2006/42 / CE. Non è necessaria alcuna nuova ispezione di sicurezza e nessuna nuova etichetta CE, motivo per cui i programmi di sostituzione e retrofitting sono spesso preferiti rispetto a sostituzioni più massicce.
Supporto software
Al momento dell'acquisto è inoltre possibile prevedere un sistema di manutenzione predittiva customizzato per il singolo sistema, in grado di fornire dati sulle condizioni del robot e del sistema. Tale monitoraggio continuo delle condizioni permette di rivelare precocemente le irregolarità nell'usura. Su questa base è possibile adottare contromisure adeguate o pianificare accuratamente la manutenzione prima che si verifichino fermi.
Total Customer Support
Tuttavia, anche la manutenzione ha i suoi limiti. Questi ultimi vengono spesso raggiunti, ad esempio, quando il sistema in cui è inserito il robot deve essere utilizzato per scopi diversi da quelli originali o convertito in un prodotto completamente nuovo. Anche in tale caso, è opportuno riutilizzare quante più parti possibile. Contrariamente a un retrofit, una revisione completa del sistema di solito implica "grandi cambiamenti nella macchina" ai fini della Direttiva Macchine 2006/42 / CE. In questo caso, anche la tecnologia di sicurezza deve essere convertita allo stato dell'arte attuale e si richiede una rinnovata certificazione CE. Yaskawa copre questa necessità con un portfolio di servizi di ingegneria e di consulenza mirati.
I programmi di retrofit e la consulenza sulla sicurezza sono parti costitutive dell’ampio portafoglio di servizi che Yaskawa ha riunito sotto la voce "Total Customer Support (TCS)", finalizzato alla manutenzione preventiva, all'assistenza, alla fornitura dei pezzi di ricambio, nonché l'ottimizzazione, l'ammodernamento e il supporto completo lungo l'intero ciclo di vita del prodotto. Le hotline telefoniche in tutti i paesi rappresentano il punto di raccolta centrale per problemi tecnici e richieste legate a ogni generazione di dispositivi Yaskawa. La formazione presso la Yaskawa Academy completa il TCS, erogando corsi di formazione base, avanzati e su misura.


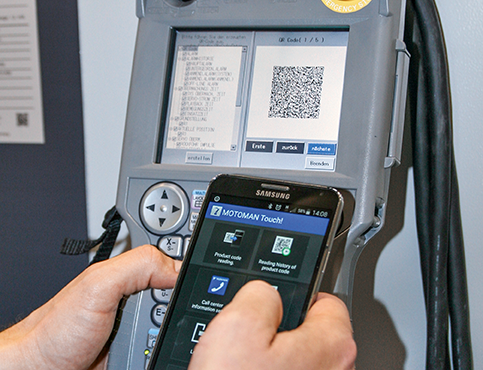
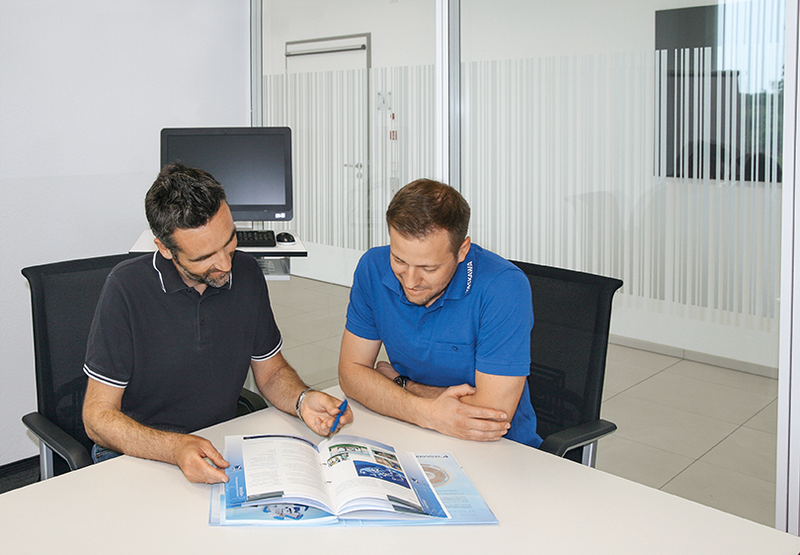
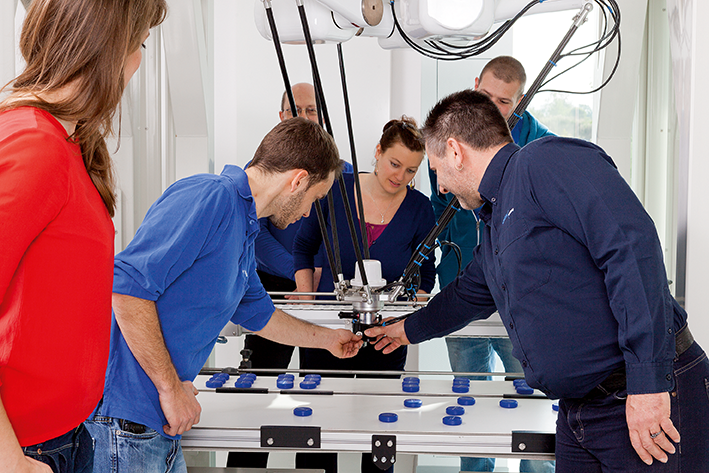