Our industry-leading, high-speed industrial robots include high-payload, extended-reach, ultra-maneuverable seven-axis and unique 15-axis dual-arm robots.
Efficienza tedesca per la produzione di mascherine
Tecnologia di automazione flessibile per la produzione di macchinari speciali
A causa della pandemia da Covid-19, è aumentata in modo esponenziale la necessità di mascherine respiratorie FFP2. Ma se all'inizio c'era una mancanza di capacità produttiva, nel corso del 2020 le cose sono rapidamente cambiate. Ingegneri meccanici esperti hanno saputo prontamente rispondere alle nuove esigenze offrendo soluzioni efficienti prodotte in Germania in un tempo sorprendentemente breve. Tra questi, il produttore di macchine speciali Unimatic Automationssysteme GmbH di Grub am Forst, vicino a Coburgo, che ha rapidamente implementato un nuovo concetto di macchina in collaborazione con Yaskawa.
Quando nel marzo 2020 è apparsa evidente la carenza di dispositivi di protezione medica, il governo tedesco ha immediatamente incaricato le aziende di produrli, anche se la maggior parte di queste non disponeva delle strutture adeguate. Unimatic Automationssysteme GmbH ha ricevuto da un cliente la richiesta di realizzare in breve tempo un sistema di produzione per mascherine respiratorie FFP2 e ha subito accettato la sfida. L'azienda si è immediatamente messa in contatto con Unimatic China. "In una joint venture con la Cina, abbiamo sviluppato il sistema e lo abbiamo adattato agli standard del mercato europeo", riferisce il dott. Robert Kahlau, responsabile del dipartimento di robotica di Unimatic. "Il cliente ha inizialmente ordinato quattro sistemi, ma l'ordine finale comprendeva un totale di otto linee di produzione".
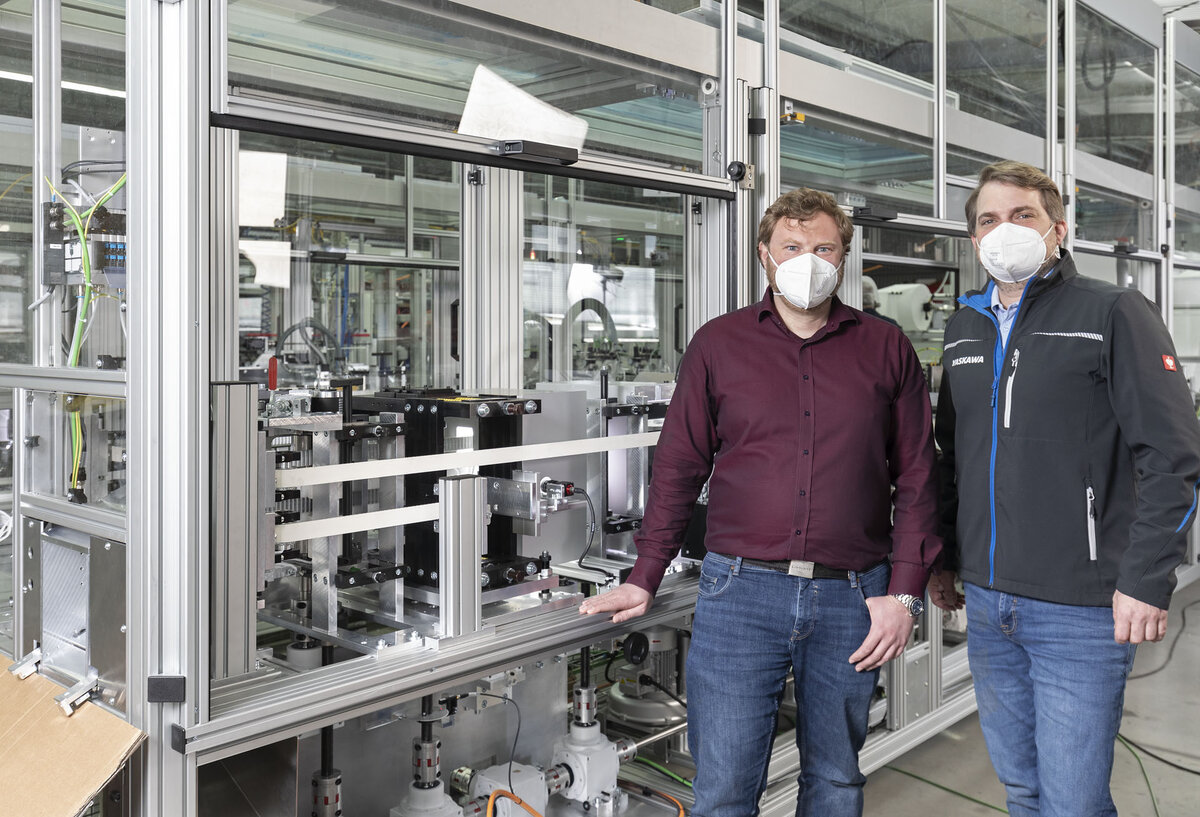
Sistema di assemblaggio completamente automatico
I sistemi di assemblaggio sono progettati per la produzione completamente automatica di mascherine FFP2 o KN95. Con una lunghezza di 10 m, una larghezza di 1,5 m e un'altezza di 2 m, i sistemi sono molto compatti e possono produrre fino 40 maschere al minuto. Tuttavia, la produzione è limitata dalle cinghie elastiche e anche il materiale multistrato con cui sono realizzate le mascherine non è semplice da lavorare. Le speciali proprietà del materiale pongono particolari requisiti a questo processo di produzione, che necessita quindi di una tecnologia di azionamento sincronizzata ad alte prestazioni.
Portare il sistema sul mercato in pochi mesi è stato un risultato eccezionale anche perché il programma era serrato e il produttore della macchina doveva evadere gli ordini pur svolgendo le sue attività quotidiane. Anche la velocità, la flessibilità e le capacità di programmazione rappresentavano delle sfide difficili. "Durante la produzione delle mascherine, abbiamo dovuto affrontare tre problemi tecnici complessi: il ‘taglio al volo’, l'elaborazione a ultrasuoni del contorno di goffratura e la tecnologia di taglio", ricorda il dott. Kahlau. “Per arrivare a una soluzione efficiente in modo rapido e sicuro, abbiamo ricercato partner competenti che ci hanno fornito le conoscenze necessarie. Abbiamo fatto molto affidamento sulla flessibilità, in particolare laddove erano necessarie decisioni rapide, e sulla disponibilità dell'intero team a cooperare, sia internamente sia con i nostri partner, al fine di completare il progetto nel più breve tempo possibile".
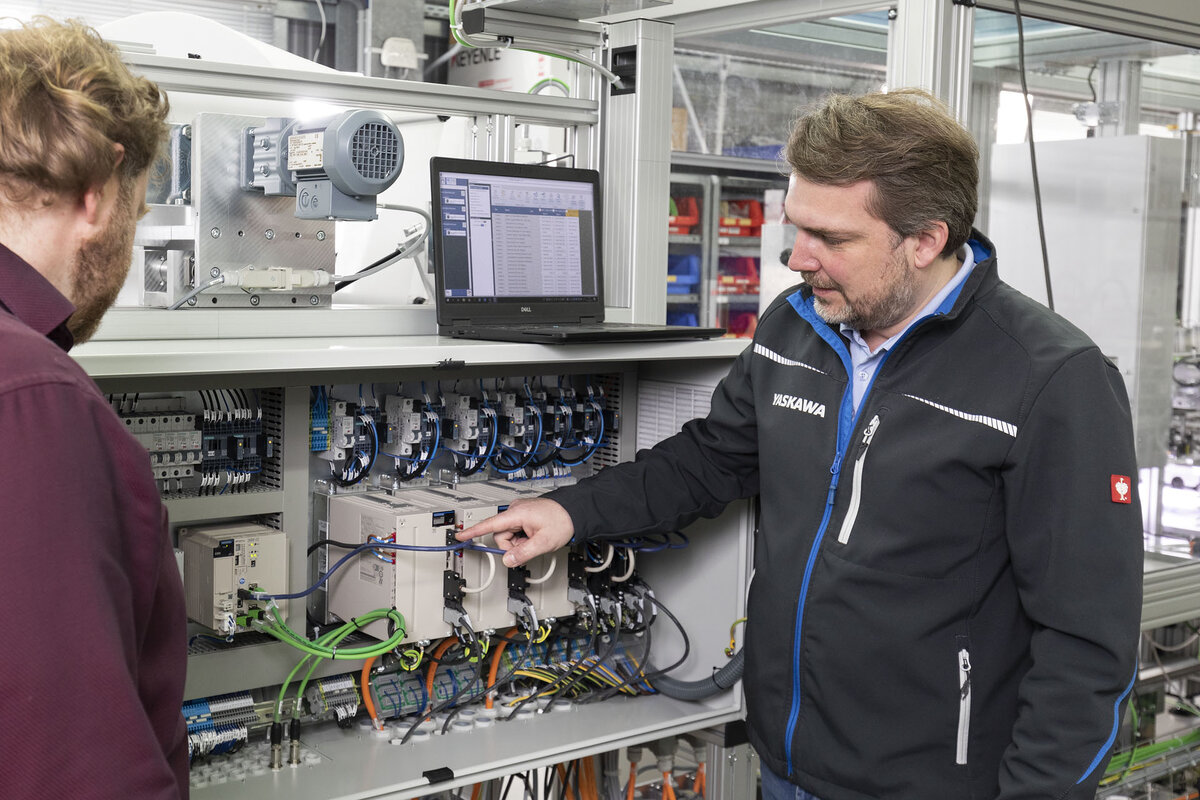
Processo di produzione fluido
Come per la maggior parte dei loro sistemi, i progettisti Unimatic hanno utilizzato un PLC Siemens per controllare la macchina. Alla ricerca della soluzione migliore per una produzione fluida, i tecnici si sono presto imbattuti in Yaskawa, di cui hanno apprezzato notevolmente il machine controller MP3300iec e i servoazionamenti Sigma-7. In particolare, il controller dispone già di librerie di funzioni integrate per il controllo a camme che possono facilmente attivare la funzione di ‘taglio al volo’. La serie di servoazionamenti è invece sinonimo di avvio rapido, elevata produttività e massima affidabilità operativa, tutti fattori ugualmente importanti per i progettisti del sistema di produzione delle mascherine. I servomotori AC reattivi coprono uscite da 50 W a 15 kW a tensioni di alimentazione di 200 V e 400 V, vantano dimensioni estremamente compatte e sono molto silenziosi durante il funzionamento. Offrono una risoluzione straordinariamente elevata (encoder assoluto a 24 bit integrato), un'elevata dinamica e funzioni come la soppressione delle vibrazioni, la soppressione delle frequenze di risonanza della macchina e la funzione tuningless per un avvio semplice. Integrando queste funzioni negli amplificatori, le loro prestazioni non sono limitate da controller di livello superiore o tempi di ciclo del bus.
"Tuttavia, non è stata solo la tecnologia a impressionarci", aggiunge Kahlau. “Lavorare con Yaskawa è stato estremamente piacevole e tutto è andato nel miglior modo possibile. L'assistenza esperta dei tecnici nella progettazione dell'azionamento, nel concetto di controllo e nel collegamento al PLC ha permesso di accelerare notevolmente il nostro progetto e, ogni volta che si presentava una sfida, veniva affrontata molto rapidamente. Qualità e competenza definiscono perfettamente questo servizio”.
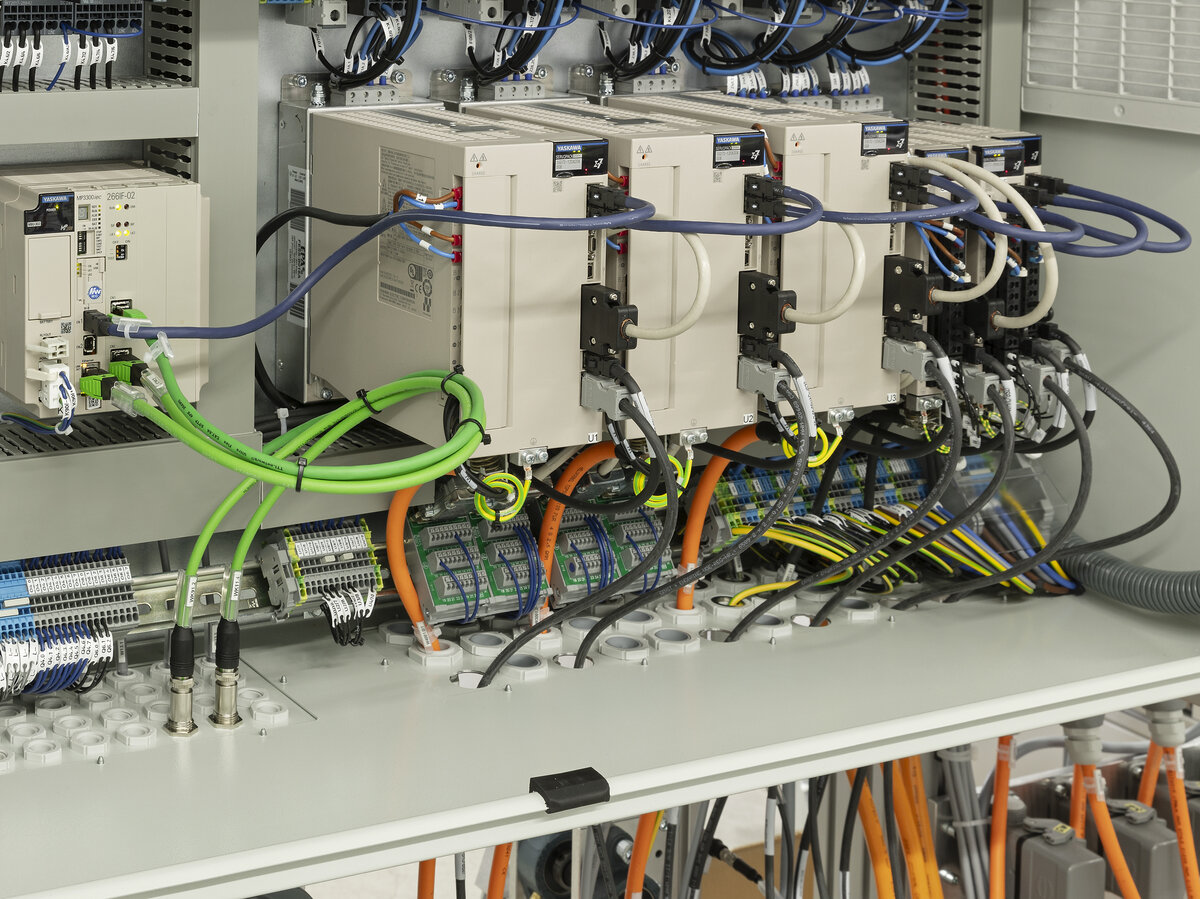
Sincronizzazione perfetta
In ogni sistema di produzione di mascherine vengono utilizzati un totale di sei servoazionamenti Sigma-7 (200 V) con potenze di motore comprese tra 200W e 1,5kW. L'azionamento più grande è quello che muove i rulli per il trasporto del materiale, mentre due motori mantengono il movimento dinamico del ‘taglio al volo’, che in questo caso comprende gli strumenti ad ultrasuoni che saldano e modellano le mascherine. Due ulteriori servoassi preparano il tessuto per la clip stringinaso. L'inserimento delle cinghie per la testa e della clip per il naso richiede un'elevata precisione di posizionamento e una sincronizzazione estremamente precisa con il tessuto.
Quest’ultima è stata resa possibile grazie al machine controller MP3300iec che comunica con i servoassi tramite il bus Ethernet in tempo reale MECHATROLINK-III, un'interfaccia ad alte prestazioni progettata appositamente per le applicazioni di movimento. Con velocità di trasmissione fino a 100 Mbps e tempi di ciclo fino a 125 µs, è possibile svolgere attività di sincronizzazione anche notevolmente più complesse rispetto al sistema di produzione delle mascherine. La programmazione è ulteriormente facilitata dallo strumento software MotionWorks IEC dotato di standard PLCopen e blocchi funzione specifici di Yaskawa (ad es. camme e ingranaggi elettronici), che sono disponibili gratuitamente e che semplificano notevolmente la programmazione del sistema. Oltre ai blocchi funzione PLCopen, MotionWorks IEC include anche funzioni come strumenti di visualizzazione, sistemi di visione, monitoraggio del nastro trasportatore e un insieme di tool a supporto del G-code. Insieme al machine controller, i blocchi funzione consentono anche il controllo di cinematiche delta e robot multiasse.
Il machine controller Yaskawa, collegato al PLC del sistema di produzione delle mascherine tramite Profinet, controlla una serie di aree tra cui la pneumatica e la sicurezza, funge da master e specifica la sequenza e il ciclo degli azionamenti. Durante la produzione in corso, il controller stabilisce i punti di trigger: se si verifica un ritardo in un punto particolare del sistema, ad esempio, la sincronizzazione si adatta a questo ritardo per evitare un'interruzione della produzione.
La soluzione elaborata con Yaskawa si è rivelata molto efficace e ha permesso di consegnare e mettere in funzione ben otto sistemi di produzione di mascherine.